About: The Process
Cast Glass
A cast glass object is one that has been formed in a mold using high heat, and is the result of a sequence of positive models and negative molds that ultimately yields the finished casting. While the process shares some similarities to the casting of other materials, such as the hot casting of metals and the cold casting of resins, concrete and engineered stone, the technical challenges to the kiln casting of glass are daunting, especially the annealing or slow cooling of the glass to relieve stress and prevent cracking, which, depending upon the shape and thickness of the glass, can take days, weeks, or even months.
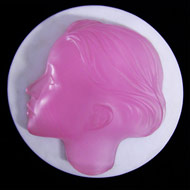
“Pretty in Pink” lifesize wall cameo by Ron Reisman
Cast glass sculpture has, over the last fifty years, steadily moved to the forefront of the art glass world, pioneered by the masters in the Czech Republic. That area of the world is considered to be to cast glass, what Murano, Italy is to blown glass. Cast glass has become some of the most prized and sought after art glass objects available.
Lead Crystal
All crystal is glass, but not all glass is crystal. Technically, for any glass to be considered crystal, it must contain a certain percentage of lead oxide. Glass that contains between 10% and 20% lead is called “demi crystal” and glass that contains between 24% and 45% lead is called “lead crystal”. The Gaffer® crystal imported from New Zealand ( recently relocated to the U.S.) that is used in the medallions has a high lead content, similar to the casting crystal used by the glass masters of the Czech Republic.
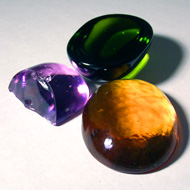
Gaffer® lead crystal billets
The British invented lead crystal in the 1700’s. They found that adding lead oxide to the glass formula increased the refractive index of the glass, making it sparkle more than glass without lead. The refractive index of a material is proportional to its density, so adding a dense metal like lead significantly increases its refractive index. The density of the lead oxide added to the glass is a double-edged sword…it increases its brilliance, but also its weight and mass. Thirty nine percent more crystal is required to fill the same space as ordinary glass. There is, however, no health issue in handling the lead crystal, since the lead oxide is chemically and physically bound in the glass.
Because lead has a relatively low melting point, lead crystal will melt and flow at a somewhat lower temperature than regular art glass, which makes it ideal for casting.
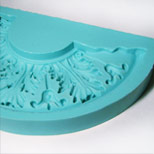
Negative silicone mold
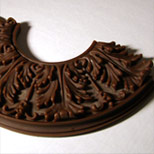
Positive wax model
The Lost Wax Process
The microcrystalline wax used to create the model of a sculpture intended to be rendered in glass has a unique property…it is solid and rigid at room temperature, but it liquefies or melts with modest heat…approximately 180 degrees F. This means that as a soft solid it can be sculpted or carved directly, or liquefied and poured into a rubber negative mold, which itself has been cast from an original model. When the wax cools, it hardens again to a solid and can be removed from the negative (reverse image) mold, retaining the exact shape and detail of the original positive model. This wax replica is now buried, or “invested” in a special refractory plaster designed to withstand the intense heat of the kiln…approximately 1500 to 1600 degrees F. However, before the negative plaster mold is ready to accept the glass and be fired, the rigid wax model must be removed. It cannot be flexed out of the hard investment plaster as with the rubber mold. This is accomplished by re-melting the wax in the mold, allowing it to flow out, leaving a perfect negative cavity of the sculpture. There are two ways to re-liquefy the wax…by burning or by steaming. Burning is dangerous because wax has a flash point, the fumes are noxious, and the fire can damage the plaster mold. A far superior way is steaming the mold…encasing the mold in a closed environment and introducing steam, which will allow the wax to gently evacuate the mold. The wax is lost from the mold in the process…hence the term “lost wax”. Any wax residue remaining in the mold will be vaporized during the subsequent drying step.
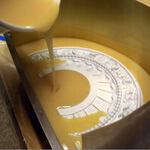
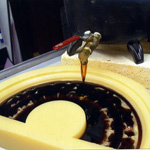
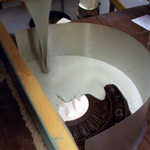
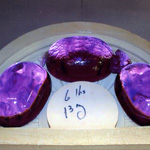
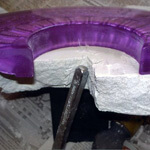

The Kiln Casting Process
The actual kiln casting of the crystal involves taking the glass from its cold, solid state to a molten state, and back to its solid state. The negative vessel that will contain the glass through this stage is called the “investment” mold. It is a mixture of various “refractory” materials (able to withstand high heat) such as alumina, silica, sand, fiberglass and plaster. (The handling of this powder absolutely requires a toxic dust respirator, since the fine powder produced contains silica particles, the inhalation of which will lead to incurable respiratory disease.) The powder is combined with the proper ratio of water, and mixed to a cake batter consistency which is then poured over and around the wax model. The proper amount of water is critical; too little and the investment mixture will be too stiff to flow and conform to every surface and detail of the model. Too much water and the strength of the hardened mold will be compromised. All of this water, up to twenty pounds, must be extracted prior to casting through a slow drying schedule (200 to 400 degrees F.) over the course of several days. If this step is rushed, the resultant steam will cause the mold to crack.
The strength of the investment mold is paramount. The extreme hydrostatic pressure of the heavy molten glass in large sculptures such as the medallions exerts tremendous force on the mold. Furthermore, the high temperature utilized converts the mold to a friable (brittle) material. If there is a catastrophic failure of the mold, the molten glass will flow unimpeded, causing devastating damage to the kiln and an extremely dangerous situation, not to mention the complete loss of very expensive crystal.
There is an important advantage to casting with crystal with a high lead content, aside from its obvious beauty. Because lead has a relatively low melting point, its addition to glass allows the glass to melt at a somewhat lower temperature than the more common sodium carbonate/limestone based art glass. While the difference between 1500 degrees F. and 1650 degrees F. might not seem that great, the difference is quite significant in terms of stress on the kiln components and the mold, as well as the energy required to reach and maintain the top temperature, or “process” temperature. (The increase of one hundred and fifty degrees at lower temperature has little or no effect on the glass, but in the upper ranges, the effect on its viscosity is substantial.
The degree to which a material will flow is called its “viscosity”. In glass casting, the viscosity of the glass must be reduced by enough heat to allow it to flow and take the exact form of the mold. The glass at casting temperature attains the viscosity similar to Blackstrap molasses. An alternative method, however, to starting the casting process with cold glass in the mold or reservoir and allowing it to melt in place, is to melt the glass in a separate special kiln called a crucible kiln, which can reach a temperature of 2300 degrees F., similar to a furnace used for glass blowing. At this temperature range, the viscosity of the glass has been reduced to that of honey, and can be poured or ladled into the mold in the casting kiln. However, with this method, the mold must be heated to at least 1000 degrees itself to prevent it from being thermally shocked by the fiery glass. And of course, full body protection is required to prevent self- immolation while the kilns are open. In addition, 1500 degrees and above reached in the kiln produces intense infra-red light, requiring the wearing of special filter glasses to prevent permanent eye damage anytime the kiln is opened or the glass observed through quartz observation ports.
At such time that the glass has filled and conformed completely to the mold, the all-important journey back to earthly temperature begins. This is the cooling or annealing phases.
Annealing of Glass
Once the cast glass begins to return to its solid state, it is still extremely hot…approx. 1000 degrees F. Glass is a very poor conductor of heat, meaning it does not shed heat quickly. The heat that is in the center of the glass, or its core, must migrate through the glass and exit from its surface. In addition, once the heat reaches the surface of the glass, it now must pass through the very insulating plaster mold which it is buried in, on its journey out to the kiln’s environment. Just as most materials expand when heated, they contract when cooled, and glass is no different in this respect. However, since the core of the glass is significantly hotter than the surface, left to its own, the cooler surface would contract faster than the core. This would produce a stressful condition in the mass of glass, as the surface tries to pull away from interior. The only way for the glass to relieve this stress is to crack. That is why the temperature of the glass mass must be brought down slowly in “baby steps”, so that the surface of the glass is never more than 5 to 10 degrees cooler than the core. The speed of this cooling, or annealing, is directly proportional to its thickness, and that schedule is exponential…a glass object that is one inch thick will take 14 hours to safely cool, but one that is eight inches thick will take 28 days! The crystal medallions spend the better part of a week in the kiln for their complete firing cycle.
The Cold Working Phase
The very careful procedure of chiseling the glass piece from the now fragile mold is the prelude to the cold working phase. Cold working of glass is any technique that is done to the glass when it is in its cold state, which might include cutting, sawing, engraving, laminating, sandblasting, acid etching, polishing, etc. For the medallions, it basically consists of three steps. The first is the correction of any defects or flaws in the casting with diamond hand and power tools. Here again, lead crystal has the advantage over soda-lime glass by being a bit “softer” to work. The second is blasting the surface with a combination of compressed air and abrasive, in this case a fine grade of aluminum oxide grit, to clean and matte the surface. The third step is a soak in a very powerful acid (again, with complete body protection and the use of an acid vapor gas mask) to seal the surface and produce the characteristic satin glow from within. After briefly neutralizing the acid with an alkaline dip, a thorough power wash completes the process.
Finally, the piece is diamond engraved with the artist’s signature, and fitted to its steel display.